Understanding the Costs: A Comprehensive Guide to Plastic Injection Molding Pricing
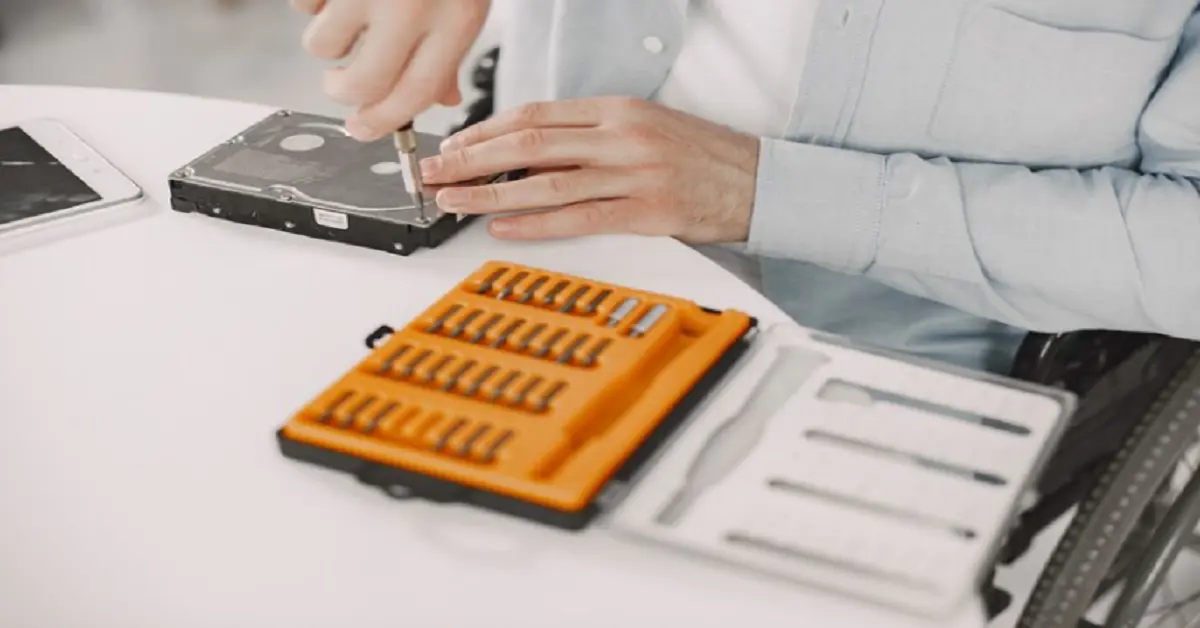
Plastic injection molding is a versatile and widely used manufacturing process that enables the production of high-quality plastic parts. Understanding the costs associated with plastic injection molding is essential for businesses looking to manage their budgets effectively and optimize production. If you need expert advice on this process, you might want to call Wunder-Mold. This guide will break down the key factors influencing pricing, helping you make informed decisions for your projects.
The Basics of Plastic Injection Molding
Plastic
involves injecting molten plastic into a mold to create a desired shape. This process is highly efficient for mass production but can vary significantly in cost depending on several factors.
Material Costs
The type of plastic material used in injection molding is a primary cost driver. Thermoplastics like polyethylene, polypropylene, and ABS are commonly used, each with different price points.
- Raw Material Prices: The cost of raw plastic material can fluctuate based on market conditions, availability, and demand.
- Material Properties: High-performance plastics with special properties, such as heat resistance or flexibility, tend to be more expensive.
The global thermoplastics market is expected to grow significantly, driven by demand in automotive, packaging, and consumer goods sectors.
Mold Design and Manufacturing
The design and manufacturing of the mold itself are critical components of the overall cost.
Complexity and Size
The complexity and size of the mold directly impact its price. A larger, more intricate mold will require more time and resources to create.
- Tooling Costs: Tooling for a mold includes the cost of designing, machining, and finishing the mold. High-precision molds with tight tolerances are more expensive.
- Multi-Cavity Molds: Molds with multiple cavities can produce several parts per cycle, reducing the per-part cost but increasing the initial mold cost.
Production Volume
The volume of production plays a significant role in determining the cost per part. Higher volumes typically result in lower per-part costs due to economies of scale.
Setup and Cycle Times
- Setup Costs: Initial setup costs for injection molding machines can be high, but these are spread out over large production runs.
- Cycle Time Efficiency: Faster cycle times reduce production costs by increasing the number of parts produced per hour.
Some modern injection molding machines can produce parts in as little as 10 seconds per cycle, drastically improving efficiency.
Additional Cost Factors
Several other factors can influence the total cost of plastic injection molding.
Post-Processing
Post-processing steps such as trimming, painting, or assembly add to the overall cost.
- Surface Finishing: High-quality surface finishes or additional treatments like UV protection or texturing can increase costs.
- Quality Control: Implementing rigorous quality control measures ensures that all parts meet specifications but adds to the production cost.
Cost Optimization Strategies
To manage and reduce plastic injection molding costs, consider the following strategies:
- Material Selection: Choosing the right material that balances performance and cost is crucial.
- Efficient Design: Simplifying part and mold design can lower tooling costs and improve cycle times.
- Supplier Partnerships: Building strong relationships with suppliers can lead to better pricing and more reliable service.
Some companies use simulation software to optimize mold designs before production, saving time and reducing costs by predicting potential issues.
The Transition to A2L Refrigerants
As the world shifts towards more environmentally friendly practices, the transition to A2L refrigerants in the injection molding industry is noteworthy. A2L refrigerants are mildly flammable but have a lower global warming potential (GWP) compared to traditional refrigerants. This transition is driven by stricter environmental regulations and the need for sustainable manufacturing processes. The use of A2L refrigerants can slightly impact the overall cost structure due to changes in equipment and safety measures, but it offers long-term benefits in reducing environmental impact. For insights into the practical applications and benefits, you can refer to Gustave A. Larson reviews. Plastic injection molding is crucial in this context as it enables the mass production of high-quality plastic components essential in various industries, from automotive to consumer goods.
Understanding the costs associated with plastic injection molding is essential for making informed decisions in manufacturing. From material selection and mold design to production volume and post-processing, numerous factors influence the overall pricing. By optimizing these elements, businesses can achieve cost-effective and high-quality production. Additionally, staying updated with industry trends, such as the transition to A2L refrigerants, can help manufacturers stay competitive and sustainable in a rapidly evolving market. Whether you are a seasoned manufacturer or new to the world of injection molding, this comprehensive guide provides valuable insights to help you navigate the complexities of pricing and achieve your production goals.
Read More: ite Nexar